Dalam persaingan ekonomi global hari ini, manufaktur tidak hanya dipacu untuk membuat produk. Manufaktur harus bisa menghasilkan daya tarik pada produk dan pelayanannya agar tidak kehilangan konsumen. Salah satu daya tarik yang mendasar adalah “kualitas”.
Kualitas adalah sebuah disiplin yang berfokus pada keunggulan produk dan pelayanan. Baik perusahaan manufaktur maupun jasa saat ini sudah mempunyai program-program kualitas. Program kualitas yang umum diterapkan adalah QA (quality assurance) dan QC (quality control). Meskipun saat ini, QA mengambil peran yang lebih besar dengan menjamin kualitas sejak dalam proses, pola lama QC masih tetap menjadi andalan.
Teknik dasar QC adalah “inspeksi”, yaitu proses pemeriksaan hasil produksi apakah sudah sesuai dengan standar dan ekspektasi konsumen. Singkat kata, inspeksi hanya kegiatan pemisahan produk dari cacat produk. Inspeksi tidak memberikan nilai tambah apa pun pada produk.
Jika manufaktur masih banyak menghasilkan produk yang tidak berkualitas, menghilangkan inspeksi (zero inspection) tidak disarankan. Di sisi lain, inspeksi pada semua produk (100% inspection) adalah proses yang mahal, khususnya untuk jenis-jenis inspeksi berikut:
- Inspeksi yang dapat merusak produk, contoh bonding test pada sepatu untuk menguji kekuatan lem antara upper dan sole sepatu.
- Inspeksi dengan biaya tinggi, contoh inspeksi item yang berjumlah sangat banyak tapi mempunyai nilai ekonomi yang rendah, seperti inspeksi kedatangan tali sepatu di pabrik sepatu.
- Inspeksi yang perlu waktu lama jika dilakukan secara sempurna, contoh inspeksi sepatu jadi berikut dengan pemeriksaan posisi penempatan sockliner pada bagian dalam sepatu.
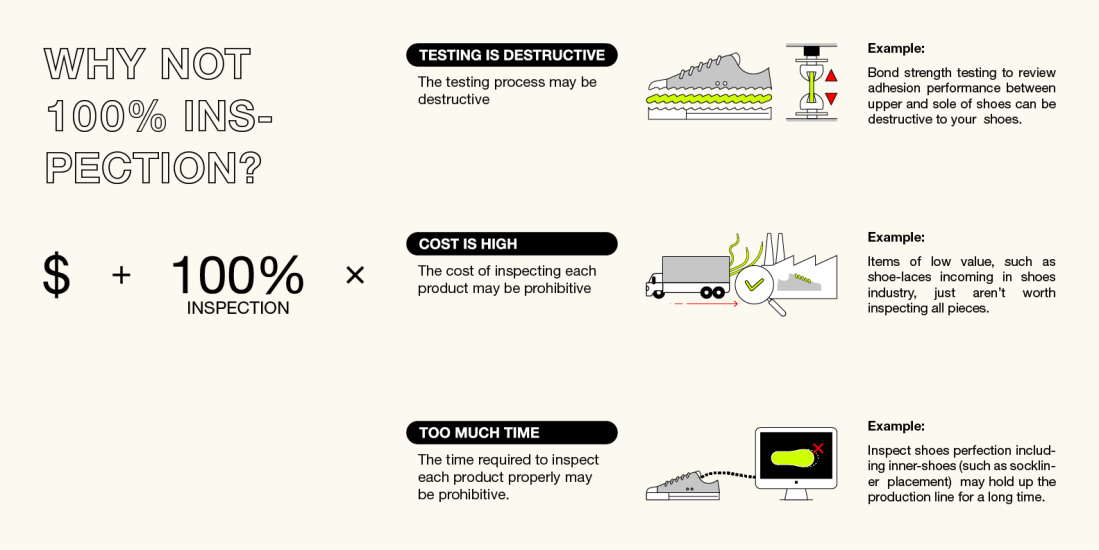
Saat inspeksi yang diperlukan dianggap mahal atau dapat merusak produk, kita dapat mengambil sejumlah sampel dari banyaknya item dalam satu lot yang akan diinspeksi sehingga inspeksi lebih efisien. Prosedur paling populer untuk menetapkan sampel dalam inspeksi kualitas adalah AQL.
Apa itu AQL?
Dalam istilah manajemen kualitas, AQL adalah singkatan dari Acceptable Quality Level (tingkat kualitas yang dapat diterima menurut produsen), atau pada standar terbaru disebut Acceptance Quality Limit (batas kualitas penerimaan).
Mengacu kepada Schilling (1999), AQL adalah tingkat kualitas yang ditentukan untuk setiap lot sehingga rencana pengambilan sampel (sampling plan) akan menerima persentase yang dikehendaki produsen (biasanya pada tingkat yang cukup tinggi di atas 95%, Pa ≥ 0.95).
Perhatikan contoh kurva Operating Characteristic (OC) pada Gambar 2. Kurva ini dibuat dari suatu sampling plan dengan nilai harapan hanya ditemukan tidak lebih dari c item cacat dari sejumlah n item sampel. Dengan distribusi Poisson, probability penerimaan sampling plan ini (lihat sumbu-y) terhadap persentase cacat (lihat sumbu-x) akan membentuk kurva, yang mana semakin kecil persentase cacat maka semakin besar probability penerimaannya, dan sebaliknya.
Produsen biasanya akan tertarik pada titik probability of acceptance (Pa= 0.95) karena punya peluang 95% lot diterima. Jika dihubungkan ke sumbu-x akan bertemu titik p1 = 2.5%. Titik inilah yang dinamakan AQL, yang mana produsen harus mempertahankan persentase cacat kurang dari AQL 2.5% sepanjang waktu agar punya peluang 95% produknya diterima.
Di pihak konsumen akan tertarik pada sisi lain kurva, yang mana persentase cacat besar harus punya probability penerimaan kecil. Dalam contoh ini, mereka tertarik pada titik Pa= 0.1 yang bertemu tingkat penolakan RQL (p2 = 7.5%). Ini berarti lot dengan persentase cacat sama dengan atau lebih buruk dari RQL hanya punya peluang terjadi 10%. Dengan kata lain, sampling plan tersebut melindungi konsumen dari kemungkinan memperoleh lot berkualitas rendah sebesar 90%.
Risiko penolakan (rejecting) lot dari kualitas AQL (p1) dikenal sebagai risiko produsen (producer’s risk), α yang mana α = 1 – Pa(p1). Hal sebaliknya adalah resiko konsumen (consumer’s risk), β yang mana β = Pa(p2). Kita menetapkan risiko ini karena kita tahu bahwa kita tidak akan selalu membuat keputusan yang akurat saat sampling dilakukan (sampling risk).

OPERATING CHARACTERISTIC (OC) CURVE
OC CURVE — A graph of percent defective, 100p (see X-axis) versus the probability that the sampling plan will accept the lot, Pa (see Y-axis).
ACCEPTABLE QUALITY LEVEL (AQL) — Poorest level of quality we are willing to accept. Example: for AQL (p1 = 2.5%), probability of acceptance is 1-α = 0.95.
REJECTABLE QUALITY LEVEL (RQL) — Quality level that is unsatisfactory and therefore should be rejected. Example: for RQL (p2 = 7.5%), probability of rejection is 1-β = 0.90.
PRODUCER’s RISK (α) — Risk of rejecting a “good” lot with a defective rate equal to AQL. In some plans, this risk is fixed at α = 0.05; in other plans, it varies from about 0.01 to 0.10.
CONSUMER’s RISK (β) — Risk of accepting a “bad” lot at RQL. Commonly, this risk is β = 0.10; this means that, at least 90% of the time, you will reject a lot with a defective rate equal to RQL.
Gambar 2. AQL dalam kurva Operating Characteristic
Untuk kemudahan negosiasi antara produsen dan konsumen, biasanya yang terbaik adalah dengan menggunakan prosedur dan standar sampling yang sudah dipublikasikan oleh lembaga standardisasi (contohnya ANSI Z1.4). Ini juga untuk menghindari masalah kredibilitas yang dibuat ketika satu pihak atau pihak lain menghasilkan sendiri prosedur dan standar sampling.
PUBLISHED SAMPLING TABLES AND PROCEDURES
Inspection by Attributes:
- MIL-STD-105E
- ANSI/ASQ Z1.4,
- ASTM E2234-09
- ISO 2859-1
Inspection by Variables: —
- MIL-STD-414
- ANSI/ASQ Z1.9
- ASTM E2762-10
- ISO 3951-1
Pada tulisan ini, saya akan mengambil contoh bentuk sederhana dari inspeksi kualitas yaitu inspeksi dengan data atribut, di mana hasil inspeksi diklasifikasikan menjadi hanya dua kelas, contoh: go/no-go, in/out, cacat/tidak cacat, dll. Di tempat saya bekerja, standar yang menjadi kesepakatan antara produsen dan konsumen/buyer untuk jenis inspeksi ini adalah ANSI/ASQ Z1.4-2003 (Sampling Procedures and Tables for Inspection by Attributes) sehingga para inspektor kami mengenalnya dengan prosedur “Tabel ANSI”.
Prosedur “Tabel ANSI”
Tujuan penggunaan AQL adalah untuk mengestimasi kualitas seluruh item (populasi), dengan cara “mencicipi” (memeriksa) hanya sebagian (kecil) item. Dengan cara seperti ini, kita dapat menghemat biaya, waktu, tenaga, dan mungkin lebih akurat dibandingkan inspeksi 100% karena inspeksi 100% rentan dengan kelelahan sehingga tidak fokus karena saking banyaknya item yang diinspeksi.
Di dalam ANSI Z1.4 maupun standar lain yang sejenis, para ahli statistik dan ahli matematika membuat sampling plan dalam bentuk “tabel pedoman” untuk memudahkan inspektor mengambil sampel yang mewakili populasi (representative). Gambar 3 berikut adalah contoh isi standar ANSI Z1.4 untuk single sampling plan (metode sekali pengambilan sampel).

Standar ANSI/ASQ Z1.4 adalah standar komersial pengganti MIL-STD-105E, yang dikembangkan oleh American National Standards Institute (ANSI) dan American Society for Quality (ASQ). Secara prosedur, ANSI Z1.4 dan MIL-STD-105E tidak ada perbedaan, kecuali dalam istilah dan penjelasan. Berikut prosedur umum menggunakan ANSI Z1.4 (Gupta & Walker, 2007, p. 192):
- Tentukan angka AQL.
- Tentukan level inspeksi.
- Tentukan lot size.
- Cari kode sample size pada Tabel I standar ANSI Z1.4.
- Tentukan jenis sampling plan (single, double, atau multiple).
- Tentukan accepted number (Ac) dan rejected number (Re) berdasarkan angka AQL dan sample size pada Tabel Master standar ANSI Z1.4.
- Terapkan switching rule.
Pada bahasan berikutnya, saya akan memberikan rincian lebih lanjut tentang prosedur umum ini beserta dengan contoh kasus inspeksi sampling di pabrik sepatu.
1. Tentukan angka AQL
Salah satu aspek terpenting dari inspeksi sampling adalah angka AQL karena angka ini mendefinisikan berapa banyak cacat yang diperbolehkan dalam suatu populasi. Angka AQL adalah rasio atau persentase cacat yang dapat ditoleransi. Semakin tinggi AQL semakin tinggi toleransi cacat. Hal ini bukan berarti kita “menginginkan (mencapai level)” adanya cacat pada barang yang yang kita inspeksi, tapi harus ada “batas penerimaan” terhadap cacat. Jadi inilah sebab beberapa lembaga standar merubah istilah “acceptable quality level” menjadi “acceptance quality limit”.
Perusahaan jasa inspeksi profesional sering menetapkan angka AQL bervariasi berdasarkan pada tingkat kekritisan produk dan karakteristik yang diinspeksi. Mereka biasanya akan mengklasifikasikan cacat produk ke dalam tiga kategori utama:
- Minor, untuk cacat kecil yang tidak mempengaruhi fungsi atau bentuk produk (tidak signifikan berbeda dengan spesifikasi konsumen).
- Major, untuk cacat yang lebih serius dari cacat minor yang mempengaruhi fungsi, kinerja, atau penampilan produk (berbeda secara signifikan dengan spesifikasi konsumen).
- Critical, untuk cacat yang sangat serius sehingga produk benar-benar tidak bisa digunakan atau berbahaya bagi penggunanya atau orang disekitarnya.
Tabel 1 di bawah ini memperlihatkan contoh pengklasifikasian cacat produk sepatu berdasarkan tiga kategori di atas.
Tabel 1. Contoh daftar klasifikasi cacat produk sepatu
Jika pasar sepatu anda adalah negara-negara yang mentoleransi cacat kosmetik, masalah tali sepatu tidak rapih mungkin dapat diklasifikasikan sebagai cacat “minor”. Namun, apabila anda mengekspor ke negara yang mempunyai toleransi rendah terhadap issue–issue kualitas (misalnya Jepang) atau ke retailer high-end, bisa jadi masalah tali sepatu tidak rapih jadi cacat “major”.
Beberapa perusahaan menetapkan angka AQL berbeda-beda untuk pasar dan harga/ jenis produk yang berbeda seperti yang dicontohkan pada Tabel 2 di bawah ini.
Tabel 2. Contoh angka AQL untuk beberapa klasifikasi cacat dan biaya produk
Pada kasus keamanan (safety) produk, 100% inspeksi/ testing wajib dilakukan dan tidak dapat digantikan dengan inspeksi berbasis AQL, contoh untuk mendeteksi patahan jarum, sepatu wajib melewati detektor logam sebelum (atau sesudah) inspeksi berbasis AQL. Untuk contoh selanjutnya, saya akan menggunakan angka AQL 0.0 (critical), AQL 2.5 (major), dan AQL 4.0 (minor).
2. Tentukan level inspeksi
Ketika memulai inspeksi berbasis AQL ini, kita perlu mempertimbangkan level inspeksi (level inspection) sesuai dengan corak inspeksi. Pada bagian pertama tabel AQL memuat dua kategori level inspeksi yaitu General dan Special (lihat Tabel 5—Kode sample size dan level inspeksi). General ada tiga level: I, II, dan III untuk penggunaan umum, dan Special ada empat level: S-1, S-2, S-3, dan S-4. Sample size meningkat dari level S-1 ke S-4, kemudian dari level I ke III.
Sebagian besar inspektor memilih inspeksi General karena dianggap cukup mewakili asumsi aman suatu kuantitas lot. Level Special baru dipilih ketika sample size kecil masuk akal untuk inspeksi/ testing yang merusak produk, atau sample size kecil dapat dengan tepat mewakili kuantitas lot yang lebih besar.
Aspek-aspek yang perlu dipertimbangkan saat pemilihan jenis dan level inspeksi dapat dilihat pada Tabel 3 di bawah ini.
Tabel 3. Pedoman untuk memilih level inspeksi
Standar ANSI Z1.4 (2008, p. 5) menyarankan menggunakan level inspeksi G-II jika tidak ada “ketentuan lain”. Level inspeksi G-II paling sering dipilih karena dipandang cukup “aman” (risiko sampling kecil) dengan biaya inspeksi yang rendah. Oleh karena itu, saya akan menggunakan level inspeksi ini untuk contoh-contoh kasus pada postingan ini.
Lalu apa maksud “ketentuan lain” (unless otherwise specified) untuk penggunaan level inspeksi selain G-II?
Level inspeksi G-I yang mempunyai sample size terkecil dari tiga level inspeksi General dapat digunakan untuk situasi di mana:
- Waktu dan anggaran untuk inspeksi terbatas.
- Untuk produk promo atau produk yang minim risiko bahaya (safety issues)
- Produsen mampu menerapkan QMS berbasis ISO 9001 dan mempunyai reputasi yang panjang dan konsisten dalam menghasilkan produk yang berkualitas.
Ada situasi di mana kita perlu meminimalkan risiko sampling dengan menggunakan level inspeksi G-III yang mempunyai sample size terbesar. Level inspeksi G-III perlu dipertimbangkan pada kasus di mana:
- Produsen mempunyai reputasi kualitas yang buruk.
- Order/ kontrak pertama dengan produsen.
- Rilis pertama dari produk yang baru dikembangkan.
- Produk bernilai sangat tinggi (barang mewah) atau memiliki risiko sangat tinggi (misal peralatan medis).
Sementara itu S-1, S-2, S-3, dan S-4 dapat digunakan jika diperlukan sample size yang relatif lebih kecil dan jika risiko sampling yang besar dapat ditoleransi.
CONTOH PEMILIHAN LEVEL INSPEKSI
LEVEL INSPEKSI G-II — Pemeriksaan fungsi produk.
LEVEL INSPEKSI S-4 — Pengukuran dimensi-dimensi penting produk (asumsi: hasil pengukuran serupa pada semua produk dalam lot).
LEVEL INSPEKSI S-3 — Testing kekuatan bonding komponen upper dan outsole sepatu (testing akan merusak sepatu).
LEVEL INSPEKSI S-1 — Pemeriksaan scan barcode.
3. Tentukan lot size
Lot size adalah jumlah item yang dipesan untuk pengiriman pada tanggal tertentu atau diproduksi dalam sekali produksi. Setiap pesanan biasanya diidentifikasi dengan kode unik yang disebut SKU (stock keeping unit). Lot size dapat ditentukan dari jumlah setiap SKU. Memeriksa banyak SKU secara terpisah dapat meminimalkan risiko sampling, tetapi akan memakan banyak waktu dan biaya.
Jika sumber daya kita terbatas, kita perlu mempertimbangkan untuk menggabungkan beberapa SKU yang sama/ mirip dan memeriksanya bersama-sama. Katakanlah dari tiga SKU berbeda dalam pesanan, terdapat dua SKU yang hanya berbeda warna, kita dapat menggabungkan dua SKU tersebut sebagai sebagai satu lot, dan satu SKU lainnya sebagai lot terpisah (lihat ilustrasinya pada Tabel 4).
Tabel 4. Menentukan lot size
Untuk lebih mudahnya dapat dijelaskan dengan contoh berikut:
Kita akan menggunakan AQL untuk memeriksa hasil produksi 600 pasang sepatu. Hasil produksi tersebut memiliki lima nomor SKU berbeda, kelimanya model yang sama dengan lima color way yang berbeda-beda, masing-masing color way tidak perlu perlakuan khusus baik secara material maupun riwayat cacat warna (migration, yellowing, dsb.) sehingga kita bisa memutuskan untuk menggabungkan nomor-nomor SKU tersebut dan memeriksanya sebagai satu lot. Jadi lot size untuk contoh kasus selanjutnya adalah 600 pasang.
4. Cari kode sample size
Setelah menentukan lot size sebanyak 600 pasang, cari lot size tersebut pada Tabel I standar ANSI Z1.4 (sebagaimana juga diperlihatkan pada Tabel 5 di bawah ini), yang pada tabel berada pada rentang 501–1200. Sorot baris ini maka kita menemukan kode huruf J pada level inspeksi G-II (lihat ilustrasinya pada Tabel 5).
Tabel 5. ANSI/ASQ Z1.4-2008 Table I: Kode sample size
Kode huruf tersebut akan kita gunakan pada “tabel master” ANSI Z1.4 untuk menarik berapa banyak item yang harus diinspeksi. Kita akan memilih salah satu dari beberapa pilihan tabel master dalam ANSI Z1.4 sesuai dengan jenis sampling plan yang akan kita tentukan.
5. Tentukan jenis sampling plan
Sampling plan adalah rencana penarikan sample size yang akan diinspeksi dan jumlah sampel yang diperbolehkan pada batas spesifikasi penerimaan sampel (acceptance number) untuk menentukan keberterimaan suatu lot. Dalam ANSI Z1.4 terdapat tiga macam sampling plan, yaitu:
- single sampling plan (ANSI Z1.4, Table II),
- double sampling plan (ANSI Z1.4, Table III), dan
- multiple sampling plan (ANSI Z1.4, Table IV)
masing-masing dengan tiga tingkatan inspeksi (inspection severity), yaitu tightened (diperlonggar), normal, dan reduced (diperketat). Sistem ANSI Z1.4 mengatur inspeksi harus dimulai pada tingkatan normal (lihat switching rule).
Single sampling plan — menerima atau menolak lot berdasarkan satu sampel saja (yang mewakili populasi).
Double sampling plan — terdapat 3 kesimpulan: menerima lot, menolak lot, dan sampling ulang. Jika sampling ulang maka hasilnya diakumulasikan dengan sampling pertama. Lot akan diputuskan diterima atau ditolak pada sampling kedua.
Multiple sampling plan — prosedurnya sama dengan double sampling plan, tetapi sampling ulang untuk mencapai keputusan dilakukan lebih dari dua kali (berkali-kali). Kemudahan sampling ini adalah sample size lebih kecil dari kedua sampling plan sebelumnya, tetapi akan menjadi rumit jika lot ditolak.
Pada contoh ini, kita akan menggunakan dasar dari semua sampling plan, yaitu single sampling plan. Single sampling plan dengan data atribut cocok untuk semua situasi sampling, paling sederhana, dan sering menjadi tolok ukur sampling plan lainnya sehingga dalam prakteknya paling banyak digunakan untuk pekerjaan inspeksi kualitas (Schilling & Neubauer, 2009, p. 113).
6. Tentukan Accepted number (Ac) dan Rejected number (Re)
Setelah memilih single sampling plan, maka tabel master yang akan kita pakai adalah Tabel II (sebagaimana juga diperlihatkan pada Tabel 6 di bawah ini). Pada tabel ini, kita akan menemukan angka AQL di baris atas tabel dan kode huruf sample size pada kolom sisi kiri. Pada kolom sisi kiri, kita dapat mengetahui sample size yang harus ditarik dari kode huruf yang sudah ditentukan di atas, yaitu: Huruf J = 80 pasang.
Tabel 6. ANSI/ASQ Z1.4-2008 Table II-A: Single sampling plan untuk inspeksi normal (Tabel master)
Setiap kolom AQL terbagi menjadi dua kolom lagi, “Ac” dan “Re”. Ini adalah kolom untuk bilangan atau batas spesifikasi penerimaan (accepted number) dan penolakan (rejected number) sampel. Jika kita menemukan jumlah cacat lebih besar dari accepted number (Ac), kita harus menolak lot berdasarkan AQL yang telah kita pilih.
Tabel 6 di atas memperlihatkan bahwa di bawah kolom AQL 2.5 persen sejajar dengan baris sample size 80 terdapat accepted number (Ac) dan rejected number (Re) yang masing-masing sebesar 5 dan 6. Ini berarti bahwa jika kita menemukan 6 cacat atau lebih dalam sampel, maka kita harus menolak (reject) lot.
Pada langkah pertama kita telah menentukan angka AQL kita adalah 0.0 (critical), 2.5 (major), dan 4.0 (minor), maka accepted number (Ac) dan rejected number (Re) pada sample size 80 untuk masing-masing angka AQL adalah sebagai berikut:
- AQL 0.0 (critical): Tidak ada toleransi untuk cacat critical. Jika ditemukan 1 cacat critical (misal sepatu berjamur) dari 80 sampel, lot sebanyak 600 pasang sepatu harus ditolak (reject) atau inspeksi 100%.
- AQL 2.5 (major): Ac = 5, Re = 6. Jika ditemukan 6 cacat major (misal jahitan rusak) dari 80 sampel, lot sebanyak 600 pasang sepatu harus ditolak.
- AQL 4.0 (minor): Ac = 7, Re = 8. Jika ditemukan 8 cacat minor (misal benang panjang) dari 80 sampel, lot sebanyak 600 pasang sepatu harus ditolak.
Ada situasi di mana saat mencocokkan sample size dengan angka AQL untuk menentukan accepted number (Ac) dan rejected number (Re), kita bertemu dengan tanda panah. Tanda panah yang mengarah ke bawah menunjukkan bahwa sample size yang lebih besar diperlukan daripada sample size yang pertama kali kita hitung. Tanda panah yang mengarah ke atas menunjukkan bahwa lot size kita berlebihan pada angka AQL tersebut, dan sample size yang lebih kecil sudah cukup memadai.
Sebagai contoh, jika AQL yang ditetapkan relatif ketat pada angka 0.065, sample size asli sebesar 80 pasang ternyata tidak memadai. Kita harus mengikuti tanda panah pada tabel yang menunjuk ke accepted number dan rejected number berikutnya (Ac = 0 dan Re = 1), di mana kita menemukan sample size sebesar 200 pasang. Ini adalah sample size terkecil yang cukup signifikan secara statistik untuk membuat keputusan pada AQL 0.065.
Ketika suatu lot ditolak berturut-turut, mungkin kita perlu membuat strategi untuk memperketat inspeksi. Atau sebaliknya, ketika suatu lot diterima berturut-turut, kita perlu melonggarkan inspeksi untuk efisiensi. Keputusan bisnis ini diatur dalam standar ANSI Z1.4 yang dikenal dengan istilah switching rule (aturan pengalihan).
7. Terapkan switching rule
Dalam ANSI Z1.4 untuk masing-masing sampling plan terdapat tiga tingkatan inspeksi (inspection severity), yaitu tightened (diperlonggar), normal, dan reduced (diperketat), yang mana:
- Normal menggunakan Tabel II-A ANSI Z1.4.
- Tightened menggunakan Tabel II-B ANSI Z1.4.
- Reduced menggunakan Tabel II-C ANSI Z1.4.
Katakanlah kita akan menggunakan AQL 2.5 untuk lot size = 600 (seperti contoh di atas), gambaran sampling plan untuk ketiga tingkatan inspeksi tersebut adalah sebagai berikut:
- Normal: Sample size = 80, Ac = 5, Re = 6.
- Tightened: Sample size = 80, Ac = 3, Re = 4.
- Reduced: Sample size = 32, Ac = 2, Re = 5.
Sistem ANSI Z1.4 mengatur inspeksi harus dimulai pada tingkatan normal, lalu kapan kita harus memperketat inspeksi? dan kapan kita harus melonggarkan inspeksi? ANSI Z1.4 mengaturnya dalam switching rule seperti pada Gambar 4 di bawah ini.
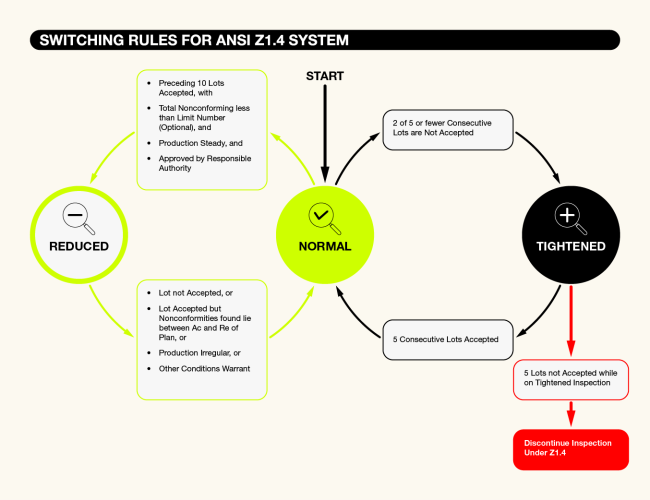
SWITCHING RULE
NORMAL KE TIGHTENED
Jika 2 dari 2, 3, 4, atau 5 lot berturut-turut ditolak selama normal inspection, maka inspeksi harus diubah ke tightened inspection.
TIGHTENED KE NORMAL
Jika 5 lot berturut-turut diterima pada saat tightened inspection, maka inspeksi dapat kembali ke normal inspection.
NORMAL KE REDUCED
- Jika 10 lot berturut-turut diterima, dengan
- Jumlah cacat (dalam 10 lot tersebut) di bawah Limit Numbers for Reduced Inspection (lihat Table VIII dalam ANSI Z1.4), dan
- Produksi dalam kondisi stabil, dan
- Telah disetujui oleh otoritas yang bertanggung jawab.
REDUCED KE NORMAL
- Jika suatu lot ditolak, atau
- Jika lot hanya sebagian dapat diterima (jumlah cacat jatuh diantara accepted number dan rejected number), atau
- Produksi tidak teratur atau sering terlambat, atau
- Kondisi lain yang mengharuskan kembali ke normal inspection.
DISCONTINUE INSPECTION
Jika 5 lot berturut-turut selama tightened inspection ditolak, inspeksi harus dihentikan sambil menunggu tindakan perbaikan terhadap kualitas produk.
Apakah switching rule ini wajib digunakan? Tidak wajib, tetapi ada risiko yang harus ditanggung:
- Risiko pertama adalah jika inspeksi tidak diperketat ketika terjadi masalah berturut-turut, maka akan ada risiko pelanggan mendapatkan produk yang buruk.
- Risiko kedua, ketika kualitas produk konsisten jika inspeksi tidak dilonggarkan, maka akan berpotensi meningkatkan anggaran inspeksi.
Switching rule ini adalah sebuah keputusan bisnis yang bertujuan untuk melindungi produsen dari risiko-risiko tersebut. Jika konsumen tidak meminta tingkat inspeksi tertentu, maka sebaiknya kita menggunakan switching rule ini.
Apakah AQL sebuah keharusan?
Andai kata pada contoh kasus di atas kita menemukan 8 item cacat dari 80 item sampel, maka artinya kita telah mendeteksi tingkat kegagalan sebesar 10%. Tingkat kegagalan 10% ini belum tentu berlaku untuk seluruh populasi, mungkin saja dalam populasi 600 item (lot size) terdapat lebih dari 60 item cacat. Tabel AQL dikembangkan secara statistik dengan tingkat kepercayaan (confidence level) tidak sampai 100% (lihat kurva OC pada Gambar 2), didalamnya mengandung risiko sampling (risiko produsen maupun risiko konsumen). Dengan kata lain, tingkat kegagalan 10% bisa berarti 1 dari 10 kali, keputusan sampling kita bisa salah dalam jangka panjang, yaitu:
- Menolak lot yang tingkat kualitasnya “bagus” sehingga muncul risiko produsen (α), misal meningkatnya biaya kualitas karena adanya 100% inspeksi, rework/ repair, scrap, dll.
- Menerima lot yang tingkat kualitasnya “buruk” sehingga muncul risiko konsumen (β), misal meningkatnya issues kualitas/ komplain, product recall, defective return dll.
AQL harus dipandang sebagai alat kontrol proses untuk mengidentifikasi rata-rata proses, bukan sebagai alat untuk memutuskan diterima atau ditolaknya suatu lot. Produsen harus mendefinisikan ruang lingkup inspeksi (level inspeksi, spesifikasi kualitas, klasifikasi cacat, dll.) dengan jelas dan tepat untuk mengukur rata-rata proses dan memperbaikinya.
Masalah lain adalah AQL dalam ANSI Z1.4 adalah turunan dari MIL-STD-105 yang dibuat satu abad yang lalu, yang mana pada abad ke-21 ini sejalan meningkatnya ekpektasi kualitas, tingkat kepercayaannya sudah tidak dapat diterima di beberapa sektor yang mensyaratkan spesifikasi kualitas yang sangat tinggi (industri dirgantara, otomotif, medis, dll.). Kebanyakan mereka menginvestasikan waktunya untuk penilaian risiko (risk assessment) dan perencanaan yang tepat untuk pengendalian/ inspeksi produk dan proses (contoh alat yang paling terkenal adalah FMEA dan Control Plan).
Standar AQL bukanlah suatu keharusan untuk mengirimkan produk yang berkualitas. Sebaiknya AQL cukup digunakan dalam kasus produk yang tidak berisiko tinggi atau kasus cacat yang tidak mempengaruhi fungsi produk. Kemampuan kita dalam penilaian risiko, perencanaan inspeksi, proses manufaktur, pemilihan pemasok, dan pemahaman terhadap harapan konsumen akan menentukan apakah masalah kualitas dapat dideteksi oleh inspektor kita atau ditemukan oleh konsumen.
Referensi
American Society for Quality. (2008). American national standard: Sampling procedures and tables for inspection by attributes (ANSI/ASQ Z1.4-2008). Milwaukee, WI: ASQ Quality Press.
Gupta, B. C., & Walker, H. F. (2007). Statistical Quality Control for the Six Sigma Green Belt. Milwaukee, WI: ASQ Quality Press.
Schilling, E. G. (1999). Acceptance sampling. In J. M. Juran, & A. B. Godfrey, Juran’s quality handbook (5th ed., pp. 46.1-46.87). New York: McGraw-Hill.
Schilling, E. G., & Neubauer, D. V. (2009). Acceptance sampling in quality control (2nd ed.). Boca Raton, FL: Taylor & Francis Group.
Webber, L., & Wallace, M. (2007). Quality control for dummies. Hoboken, NJ: Wiley Publishing, Inc.
Subhanallah…saya Followers setia blog kang Eris buat belajar teknik industri. Semoga Sukses selalu kang, terimakasih atas ilmu nya.
LikeLike
very well infonya mas, terima kasih ya. cukup menjawab pertanyaan-pertanyaanku selama ini. Sukses selalu 🙂
LikeLike
Terima Kasih telah berbagi mas, sangat rinci dan lugas.
LikeLike
Terima kasih Pak Eri Kusnadi, ilmunya sangat bermanfaat, Pak apakah bisa dibahas mengenai SQRT (n+1) dan bagaimana menentukan kriteria AQL dan RQL nya..terima kasih
LikeLike